What is Film Faced plywood?
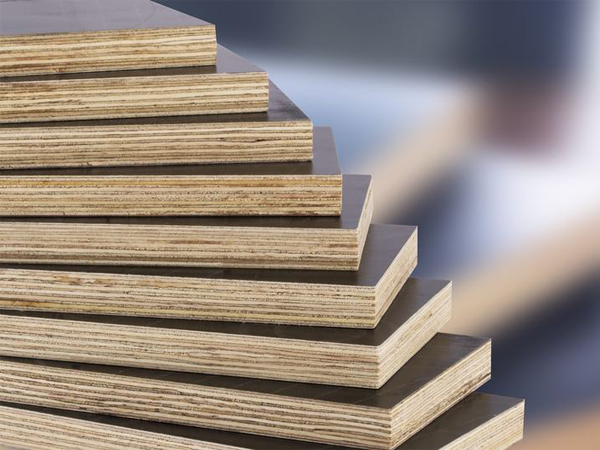
Film faced plywood, belonging to the Construction plywood system, is a combination of plywood layers and film layers applied to both surfaces under the pressure of high-frequency heat presses
Film faced plywood, belonging to the Construction plywood system, is a combination of plywood layers and film layers applied to both surfaces under the pressure of high-frequency heat presses. The product is primarily used as formwork in construction sectors: high-rise projects, residential buildings, workshops, and urban constructions. It is considered easy to transport and flexible in cutting according to concrete mold sizes.
How is film faced plywood constructed?
This type of wood consists of three parts: glue layer, wood core, and film layer. Specifically, each part is as follows:
Glue layer: The adhesive layer is a crucial component that largely determines the water resistance of the plywood. Therefore, the most commonly used adhesive is WBP waterproof glue. WBP glue with phenol or melamine content is mixed in accordance with international standards to enhance the product's water resistance. The commonly used mixing ratio in Vietnamese factories is blending WBP with Melamine at a ratio of 12% Melamine and 88% MR or 15% Melamine and 85% MR. If the glue quality is not ensured, the plywood will delaminate after 2-3 uses.
Wood core: The second part and also the factor that determines the load-bearing capacity and durability of the plywood is the wood core. This core part is often made from natural woods such as hardwood and naturally grown woods (teak, rubber wood, etc.). This is a common raw material for producing various types of plywood and finished wood products on the market, with the advantage of high durability and excellent termite resistance.
Film layer: The type of film used is Dynea phenolic film. This thin plastic film is coated on the surface of the plywood to create a glossy finish, reduce scratching, increase elasticity, increase stiffness, and provide absolute moisture resistance.
Characteristics of film faced plywood:
Flat surface, waterproof and non-absorbent to concrete, thus maintaining a smooth, even, and crack-free concrete surface upon completion.
Lightweight, easy to transport, simpler cutting and installation, thereby saving labor and construction time costs.
Reusable for economic efficiency, can be used 7-12 times depending on the construction unit and the carefulness of the workers.
High load-bearing capacity, ensuring absolute safety in construction.
Easy transportation, easy connection of plywood sheets without causing pollution to the environment.
Applications of film faced plywood:
Used as formwork in high-end construction projects such as hotels, high-rise apartments, villas, industrial projects, and transportation tunnels.
Lining for container floors, ship floors.
Stages for event organization, etc.
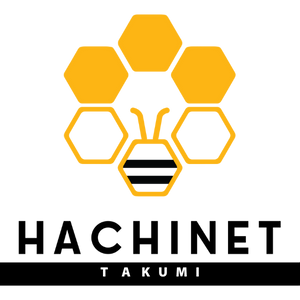