Production Process and Application of Plywood Types in Construction
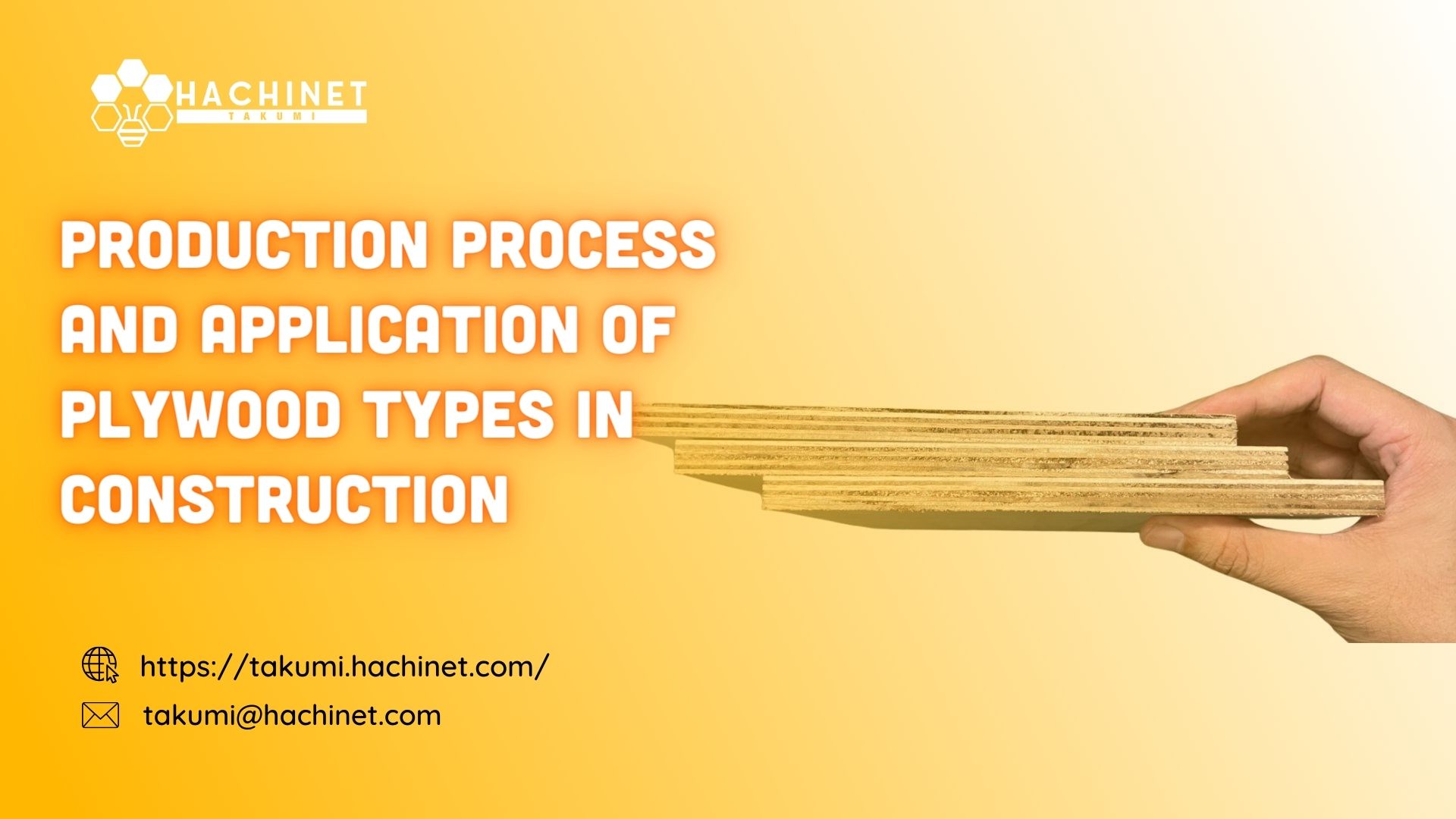
Plywood, MDF (Medium Density Fiberboard), and OSB (Oriented Strand Board) are popular construction materials known for their durability, lightness, and ease of use. Each type has its own production process and applications, ranging from floors and partitions to furniture and roofing. Choosing the right type can enhance efficiency, save costs, and ensure project quality.
Plywood
Plywood is produced from many thin layers of wood (veneer) glued together with glue. Wood materials are often chosen from trees such as pine, birch, or oak. After choosing the right type of wood, the wood will be cut into thin veneer sheets with a thickness of 1 to 3 mm. After cutting, the veneer panels are dried to remove moisture, helping the glue adhere better and preventing future warping. The drying process is usually done using an oven or drying naturally. Drying ovens use high temperatures and circulating air to quickly remove moisture in the veneer. Natural drying takes advantage of sunlight and wind, but drying time will be longer and depends on weather conditions. When the humidity has reached the standard or required level, the veneer panels are coated with phenol-formaldehyde or urea-formaldehyde adhesive to increase moisture resistance and durability.
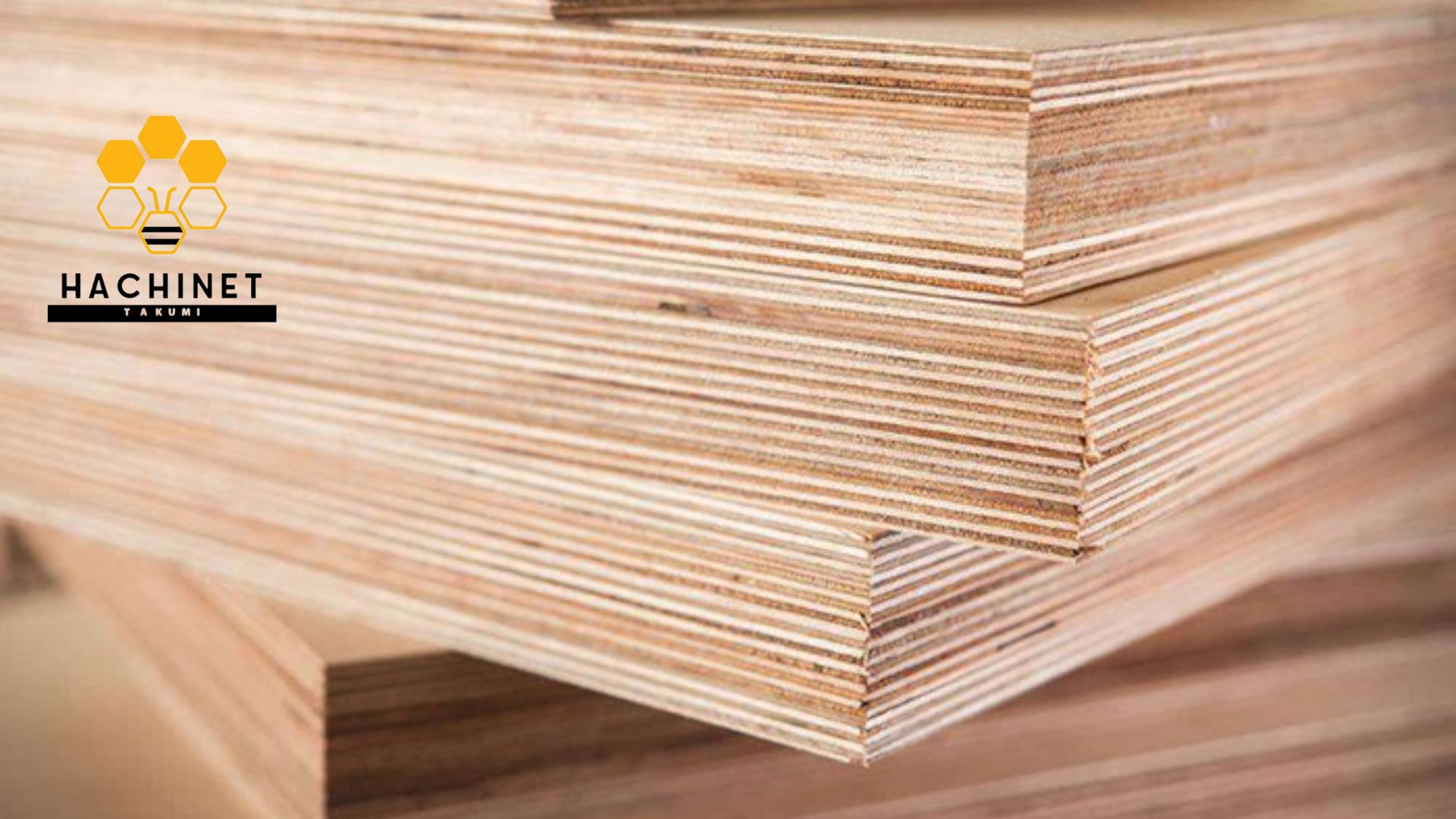
The veneer panels are stacked in a perpendicular direction, enhancing durability and load-bearing capacity. The veneer layers are pressed under high pressure (about 1,000 psi) and high temperature (about 140°C) for several minutes to several hours, depending on the type of glue and the thickness of the board. After pressing, the plywood is cut into standard sizes and the surface is sanded or coated with a finish.
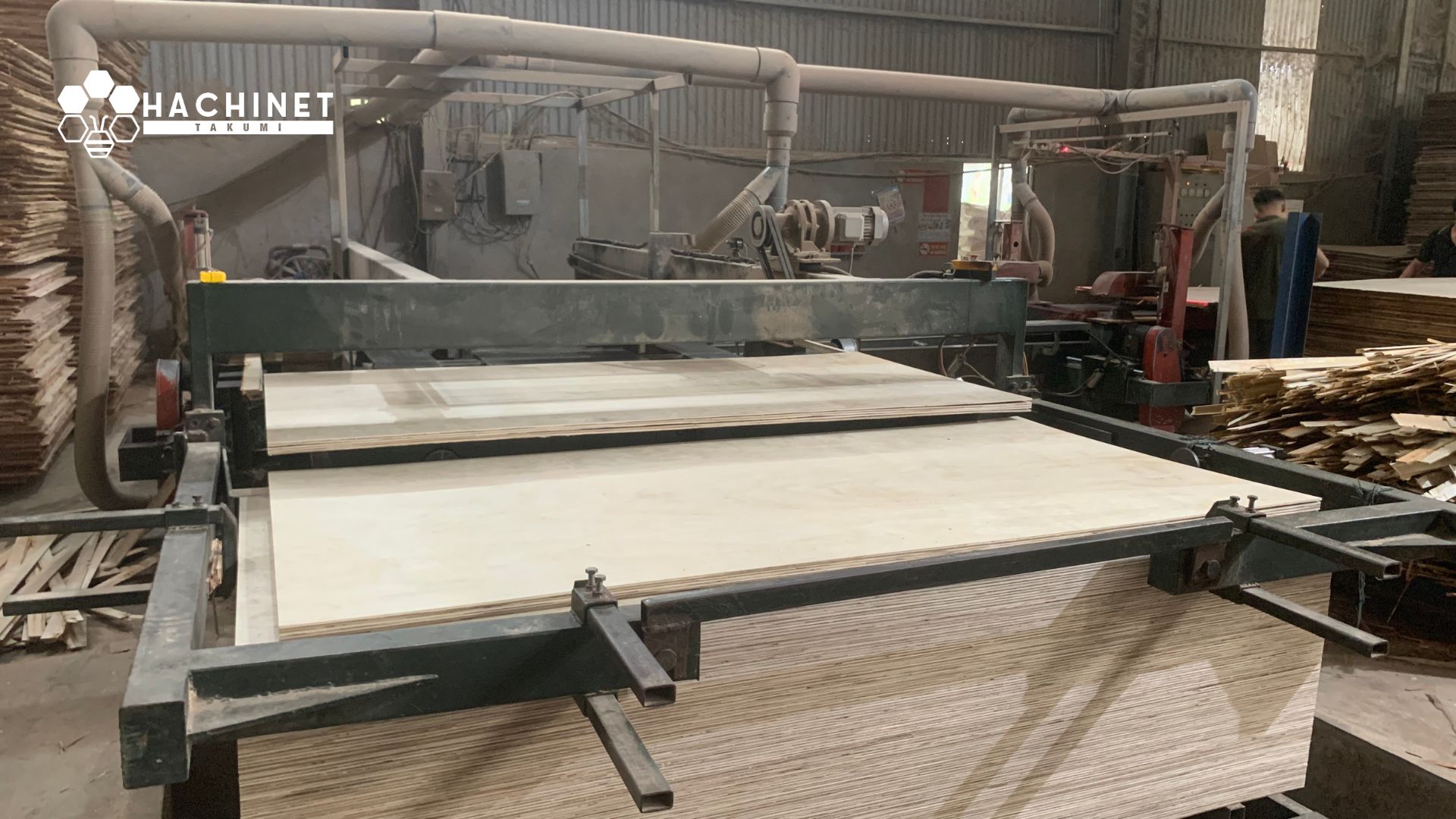
The characteristic of this type of plywood is that it is highly durable because the veneer layers are stacked perpendicularly and pressed under high pressure. Plywood has very good bearing capacity and warp resistance. With good moisture resistance With a water-resistant glue layer, plywood can withstand wet conditions, suitable for outdoor applications or in humid environments. And easy to process, users can cut, drill, and mount easily, suitable for many different applications in construction and furniture manufacturing.
MDF Plywood (Medium Density Fiberboard)
Unlike Plywood, MDF Plywood is produced from small wood fibers, combined with glue and pressed under high pressure and temperature. The main raw materials are wood chips, tree branches, or other types of wood that cannot be used in the solid wood industry. The selected wood needs to ensure appropriate quality and moisture. Then, the wood is put through a crusher to separate into small wood fibers. This process helps create fibers of uniform size, enhancing adhesion when mixed with glue. After grinding, the wood fibers are put into a drying oven to remove moisture. Drying is usually done in an oven at high temperatures and uses circulating air to quickly remove moisture. This process ensures that the wood fibers reach the ideal moisture content, helping the glue adhere better and enhancing the durability of the MDF board. The dried wood fibers are mixed with urea-formaldehyde or melamine-formaldehyde glue in a high-capacity mixer. Glue helps bind the wood fibers together, forming a homogeneous mixture. The ratio of glue and wood fiber must be strictly controlled to ensure product quality. After being mixed, the wood fiber and glue mixture is spread evenly on the conveyor belt and compressed into sheets before being put into the press. This process helps shape the initial size and thickness of the MDF board.

Next is the heat pressing process, the composite panels are pressed under high pressure (about 600-800 psi) and high temperature (about 150-180°C) for about 5 to 20 minutes. This heat pressing process helps activate the glue, bonding the wood fibers together firmly and creating MDF boards with the desired thickness and durability. After pressing, the MDF panels are cooled and allowed to stabilize to ensure that they retain their shape and size. After pressing and cooling, the MDF panels are cut into standard sizes and the surface is ground to achieve absolute smoothness and flatness. The surface of the MDF panel can then be painted or applied with surface finishes such as veneer or laminate, to increase aesthetics and durability.
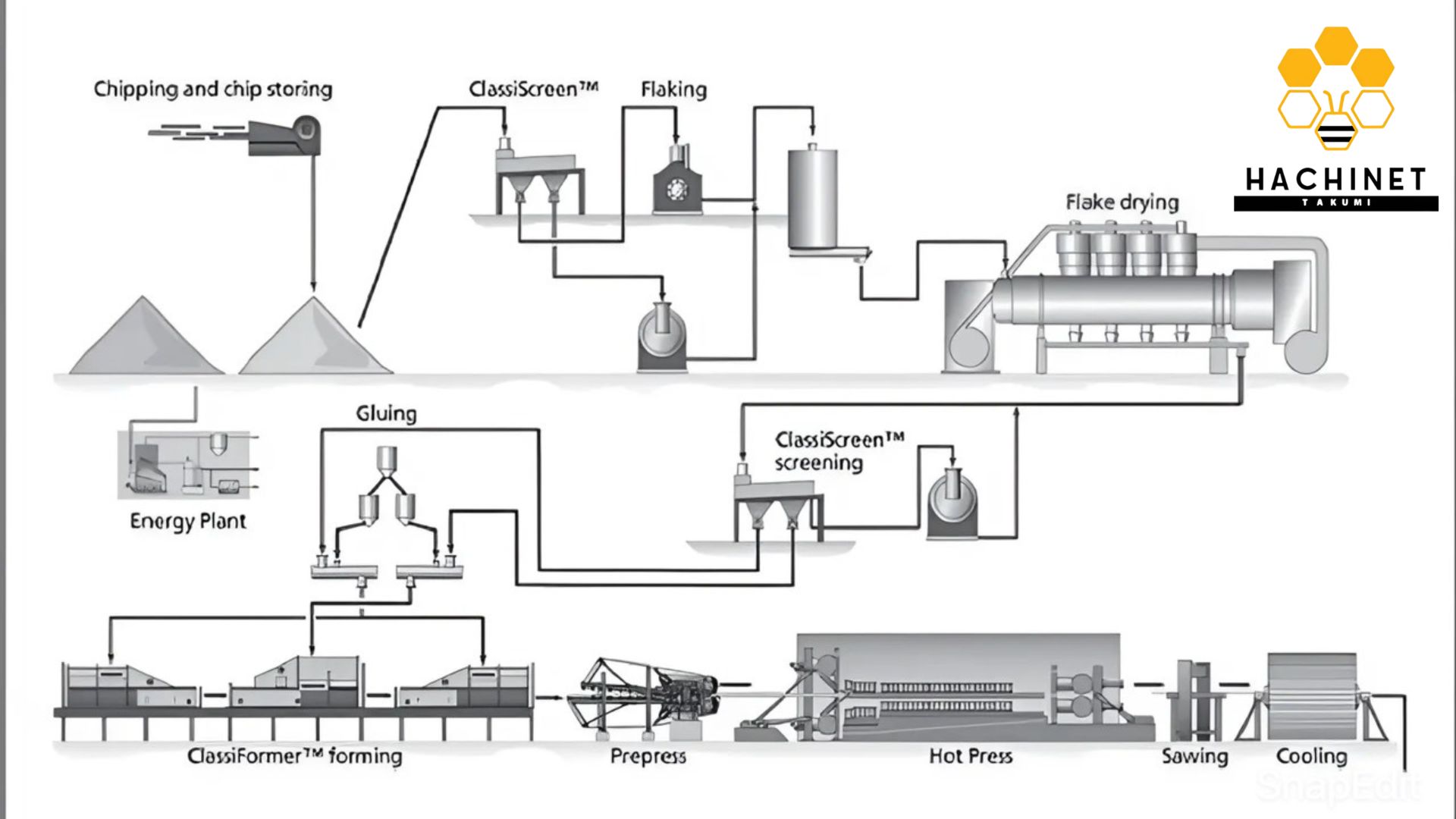
The characteristic of this type of wood is the smoothness of the surface. The surface of MDF board is smooth and uniform, very suitable for painting or decorative veneering. But MDF only has average durability, durable enough to Used in interior applications but not as strong as plywood in terms of strength and moisture resistance. MDF is easy to cut, drill, and shape, making it suitable for complex furniture production.
OSB Plywood (Oriented Strand Board)
OSB (Oriented Strand Board) plywood is produced from large wood chips, stacked in a certain direction and glued. The main raw materials are young wood, scrap wood, or recycled wood from industrial wood sources. These woods are usually pine, birch, or other hardwoods. These woods are usually pine, birch, or other hardwoods. The wood is put through a cutting machine to form small wood chips, 15 to 25 cm long and 1 to 5 cm wide.. This process ensures that the wood chips are uniform in size, helping to enhance the bond and durability of OSB boards. After that, the cut wood chips are put into a drying oven to remove moisture. The drying process is usually carried out in an oven at high temperatures. Drying helps reduce the moisture content of wood chips to an ideal level, ensuring better adhesion and increasing the durability of the final product. The dried wood chips are mixed with phenol-formaldehyde or isocyanate glue in a high-capacity mixer. Glue helps bond the wood chips together, forming a uniform mixture. The ratio of glue and wood chips must be strictly controlled to ensure product quality.
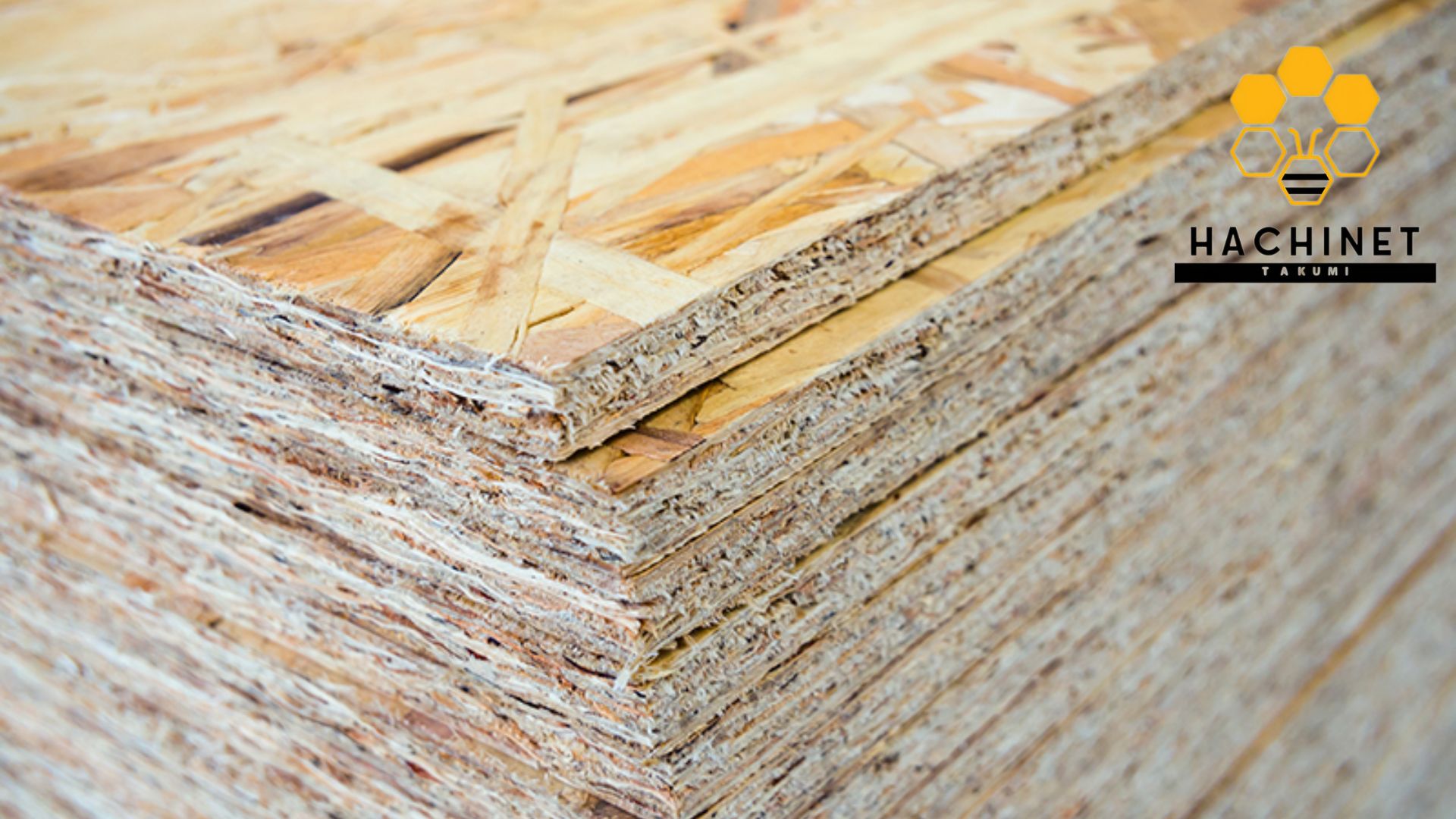
After mixing the glue, the wood chips are stacked in parallel and perpendicular directions, forming a sturdy structure. This layering is done on a conveyor belt, where the layers of wood chips are spread evenly and arranged in a certain direction to enhance the durability and load-bearing capacity of the OSB board.
The mixture of wood chips and glue is pressed under high pressure (about 1,000-1,500 psi) and high temperature (about 170-200°C) for about 5 to 10 minutes. This heat pressing process helps activate the glue and bond the wood chips together firmly, creating OSB boards with the desired thickness and durability. After pressing, the OSB panels are cooled and allowed to stabilize to ensure that they retain their shape and size. After pressing and cooling, OSB panels are cut into standard sizes. The surface of OSB panels can be coated with a waterproof layer or other finish to increase aesthetics and durability.
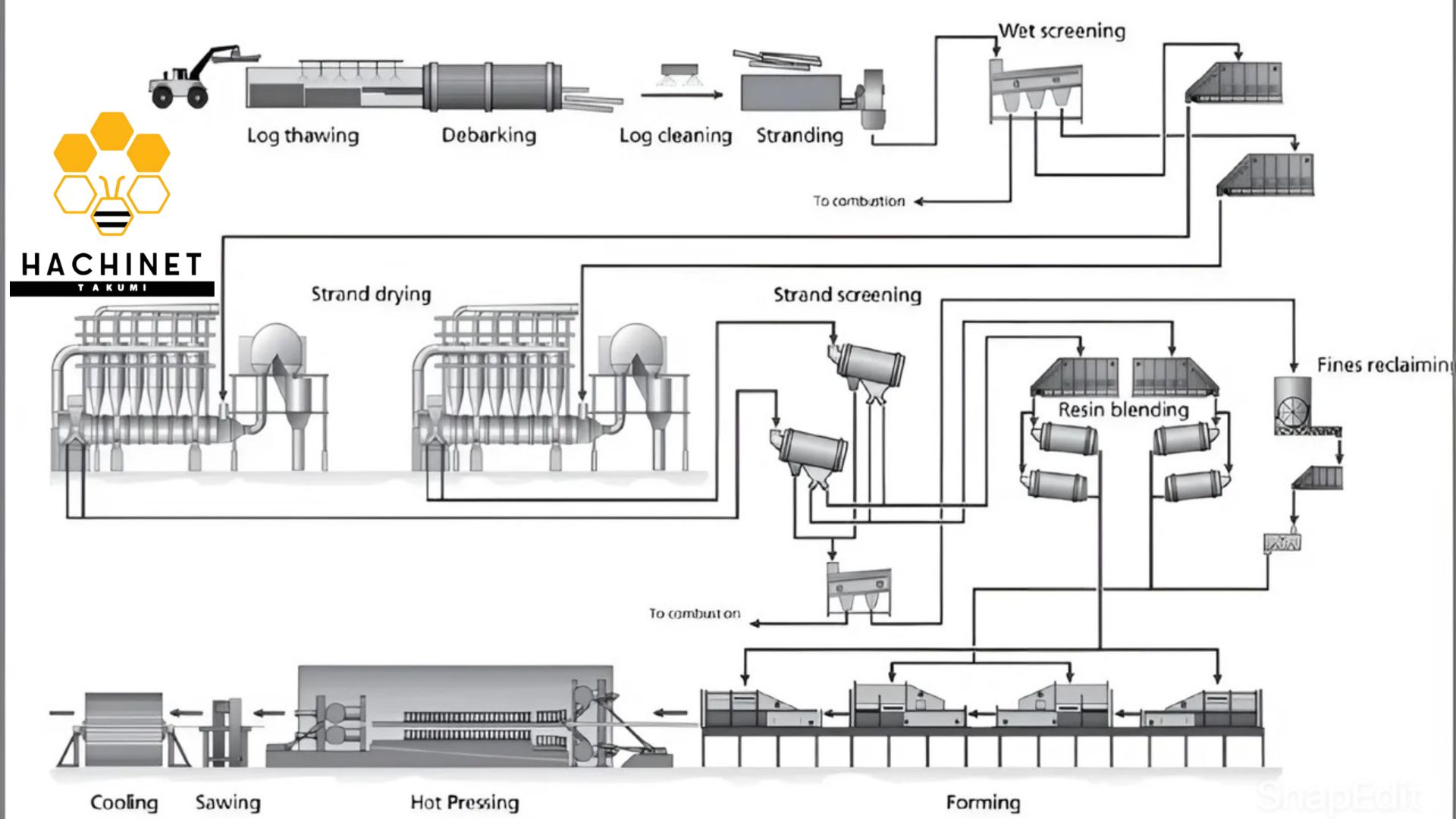
This type is highly durable: OSB's layered structure gives it good load-bearing and warping resistance, suitable for high-load applications. With water resistance: With a water-resistant adhesive layer, OSB can be used in wet environments without blistering or damage. Compared to plywood, OSB has a lower price, making it an economic choice for many construction projects.
Plywood plays an important role in the construction and furniture manufacturing industry thanks to its outstanding and diverse properties. Plywood, MDF and OSB each have their own production process, from choosing wood, grinding or cutting chips, drying, mixing glue, heat pressing, to finishing the product. Each type of plywood has its own characteristics and advantages, from high durability, moisture resistance, to easy processing, serving many different applications such as floors, partitions, roofing and furniture.
Choosing the right type of plywood not only helps increase work efficiency but also optimizes costs and ensures the quality of projects. Understanding the production process and characteristics of each type of plywood will help you make more informed decisions in using and applying them to construction and furniture production projects. Hopefully this article has provided you with useful information about types of plywood and their applications in construction.
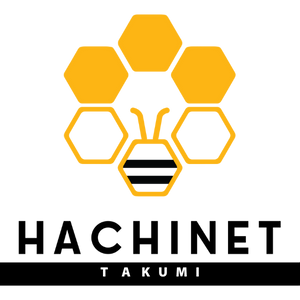