The process of manufacturing and preserving veneer
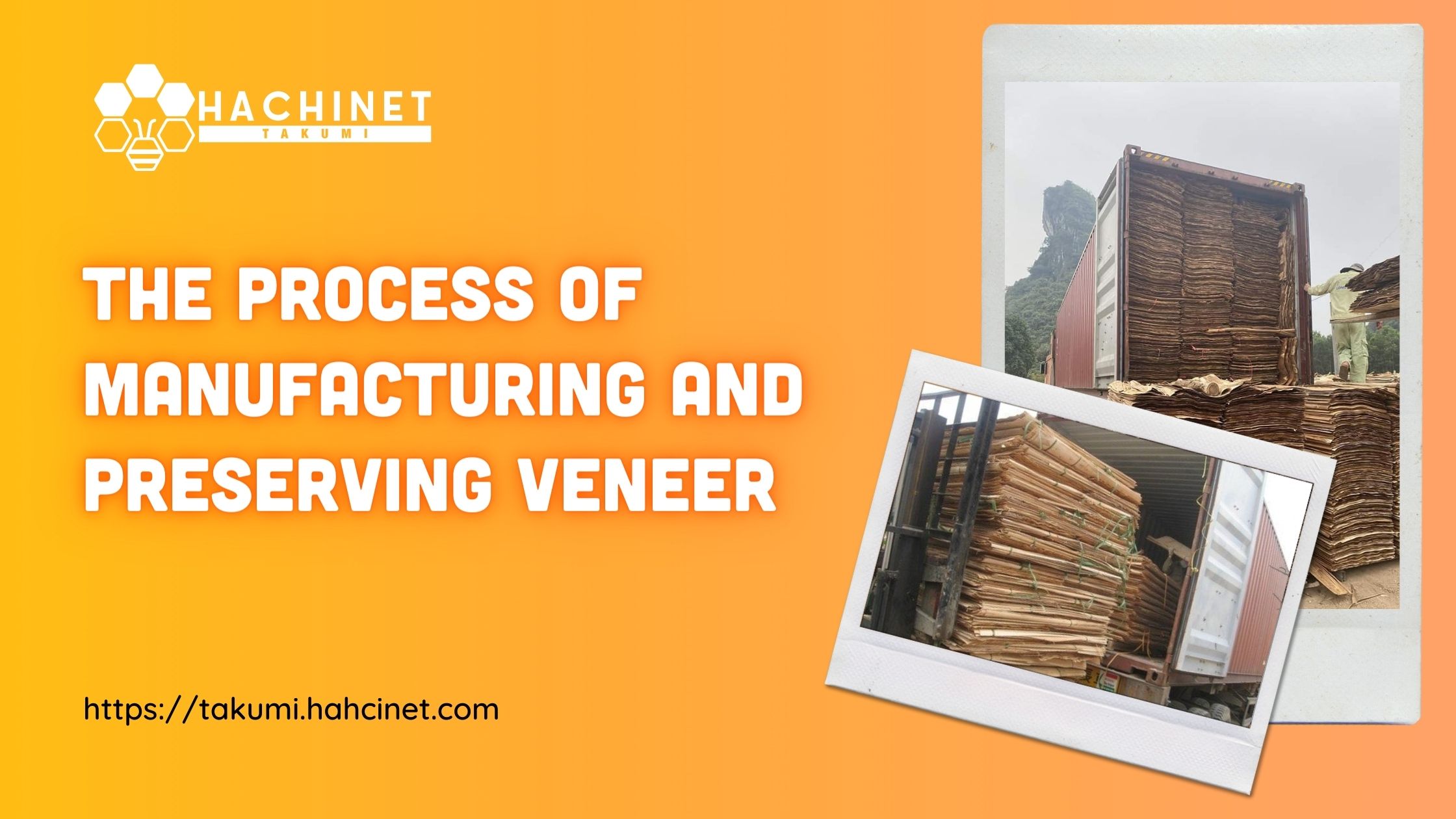
The demand for plywood veneer is increasing rapidly, leading to higher requirements in both manufacturing technology and raw materials. As a crucial material determining the quality of the finished wood panel, veneer must undergo strict processing and preservation. Depending on the characteristics of the original wood type, the thin veneer layers will be processed under different conditions.
1 . Harvesting Timber for Veneer Production
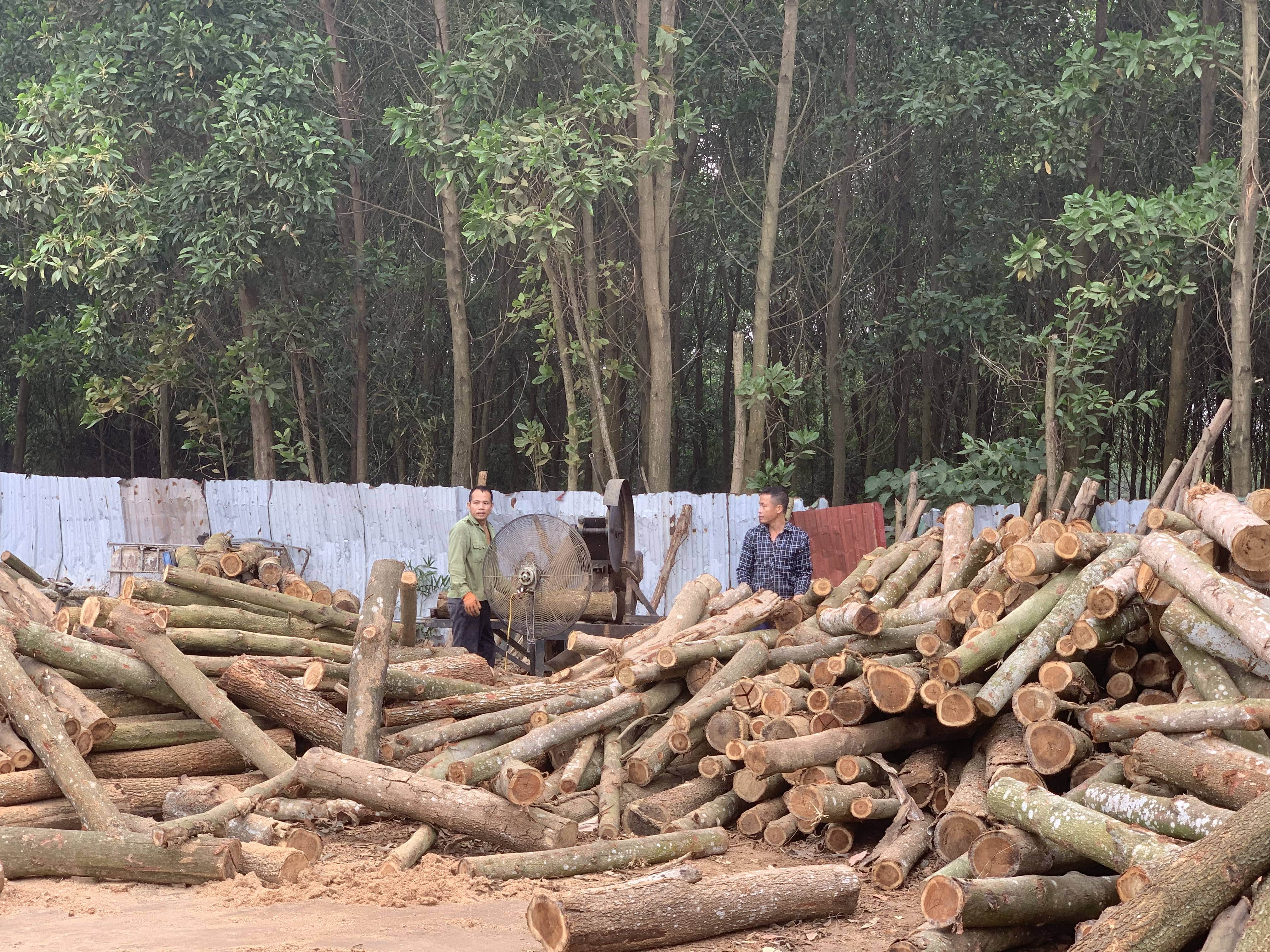
Veneer is thin sheets of wood peeled from natural timber with thickness ranging from 1 - 10mm and dimensions depending on its intended use. Typically, industrial wood species with tall, straight trunks, fewer branches, reasonable cost, and fast growth time are used for veneer production. Specifically, the harvested wood must meet FSC certification standards to bring economic value and protect the environment.
In Vietnam, many FSC-certified plantations possess various short-term industrial tree species for timber extraction to serve veneer manufacturing. Depending on each type of wood, there are specific harvesting standards. For example, plantation acacia wood over 10 years old, with a small diameter less than 15cm, and still fresh, is permitted to be felled. For rubberwood, trees aged 25-30 years, straight and tall, are eligible for extraction after completing the latex tapping cycle.
With higher prices, hardwood plywood or softwood plywood also have higher requirements for roundwood materials. Acacia wood cultivated for 5-7 years, with straight, round trunks and few defects, will be harvested. Meanwhile, pine trees require longer growth time, being harvested at around 25 years old.
2 . Preliminary Roundwood Preservation
Freshly harvested roundwood is transported to the factory and stored for a certain period before being used in veneer production. During this stage, roundwood must be properly preserved to avoid damage from insects, temperature, and humidity.
Usually, there are two common preservation methods: manual and chemical treatment. The most common manual method is soaking the wood in water, which saves costs, requires less technical expertise, and ensures the workers' health. However, it takes a long time to remove a large amount of resin and nutrients from natural wood, usually 6-12 months depending on the wood type.
Therefore, chemical treatment methods are encouraged due to their ability to process large amounts of wood in a short time. Chemical formulations are applied to prevent termite growth, sprayed evenly on the wood surface and both ends. The soaking time for the wood to absorb the chemical solution usually ranges from 24-72 hours depending on the wood type. When applying this preservation method, workers need to be fully equipped with protective gear to ensure health and strict waste handling before disposal into the environment.
3 . Wood Cutting into Sections
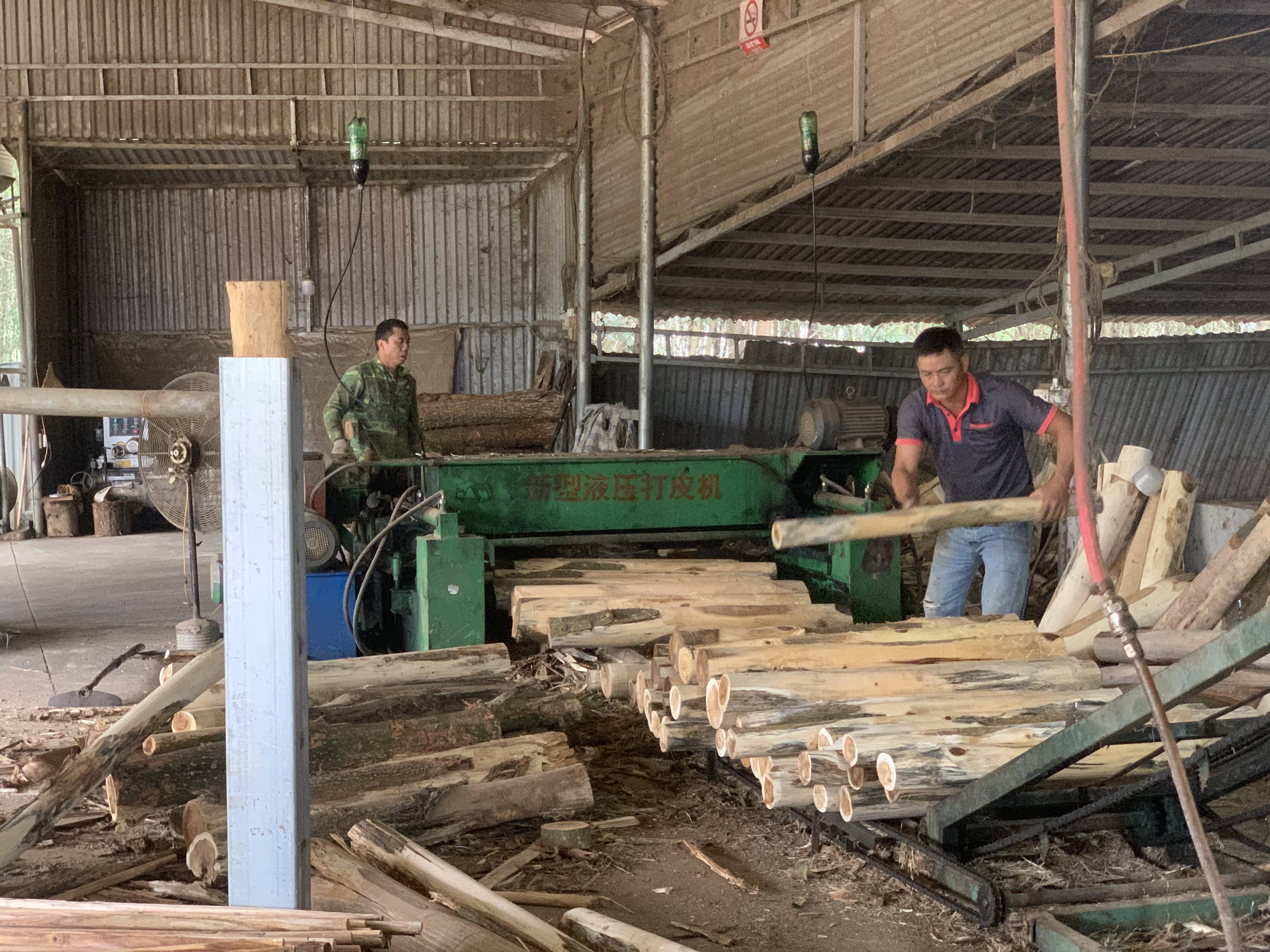
Wood transported to the workshop will be cut into sections of predefined dimensions. Simply put, this is the stage of cutting long roundwood into shorter wood sections. Typically, wood is cut into 2.6m lengths automatically, ensuring both ends are flat and smooth, reducing discrepancies between wood sections.
4 . Peeling Bark & Rounding Wood Sections
Then, the wood sections are peeled of bark and rounded by removing edges and excess branches.
5 . Thermal Treatment
Before plywood veneer production, to make the wood more pliable, resilient, and facilitate peeling, the roundwood sections need to undergo thermal treatment, either boiling or steaming depending on the wood's characteristics. The temperature and moisture levels are monitored and adjusted continuously during the thermal treatment process.
The specific boiling or steaming time depends on several factors such as:
- Final temperature
- Diameter of wood sections
- Temperature difference between wood sections and the heating environment
- Wood grain direction
- Temperature variation of wood sections
6 . Veneer Peeling and Cutting
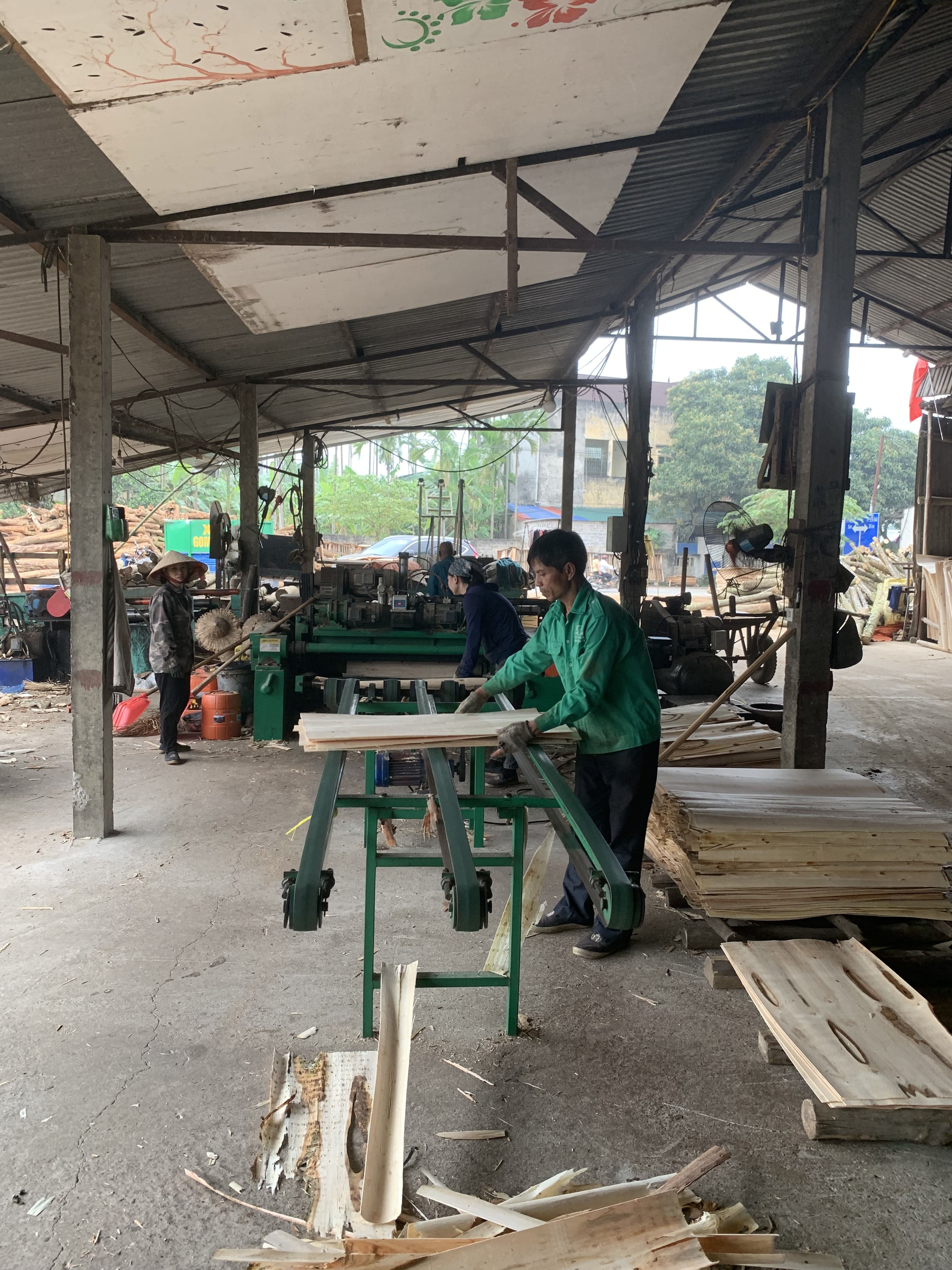
Wood softened by thermal treatment is then fed into the veneer peeling line. The size of each veneer sheet is adjusted according to the final plywood specifications. Nowadays, various veneer peeling methods are applied in different manufacturing plants: rotary cutting, quarter cutting, flat slicing, rift cutting, etc. Each peeling method yields veneer sheets with different grain patterns, such as cathedral, straight grain, curly, etc.
At Hachinet Takumi, rotary peeling is the primary veneer peeling method used. This method is performed by a peeling machine with sharp blades, peeling veneer from the outer to the inner core until the wood section is completely peeled.
7 . Veneer Preservation
Depending on the temperature and humidity conditions of the surrounding environment, veneer sheets stored for more than 1 month need to be preserved using chemicals. Veneer sheets are immersed in a solution of preservatives for a specified period and dosage.
8 . Drying
Preserved veneer sheets are continuously dried until they reach a moisture content of 8-12%. After leaving the drying machine, the veneer sheets are cut to the specified size. A dried veneer sheet meets requirements when:
- Moisture content is uniform
- No warping at the edges
- No cracks or splits
- Surface is smooth for adhesive application
- Color meets requirements
- Little to no shrinkage
Veneer drying is crucial for producing hardwood plywood, softwood plywood, etc.
9 . Sorting and Packaging
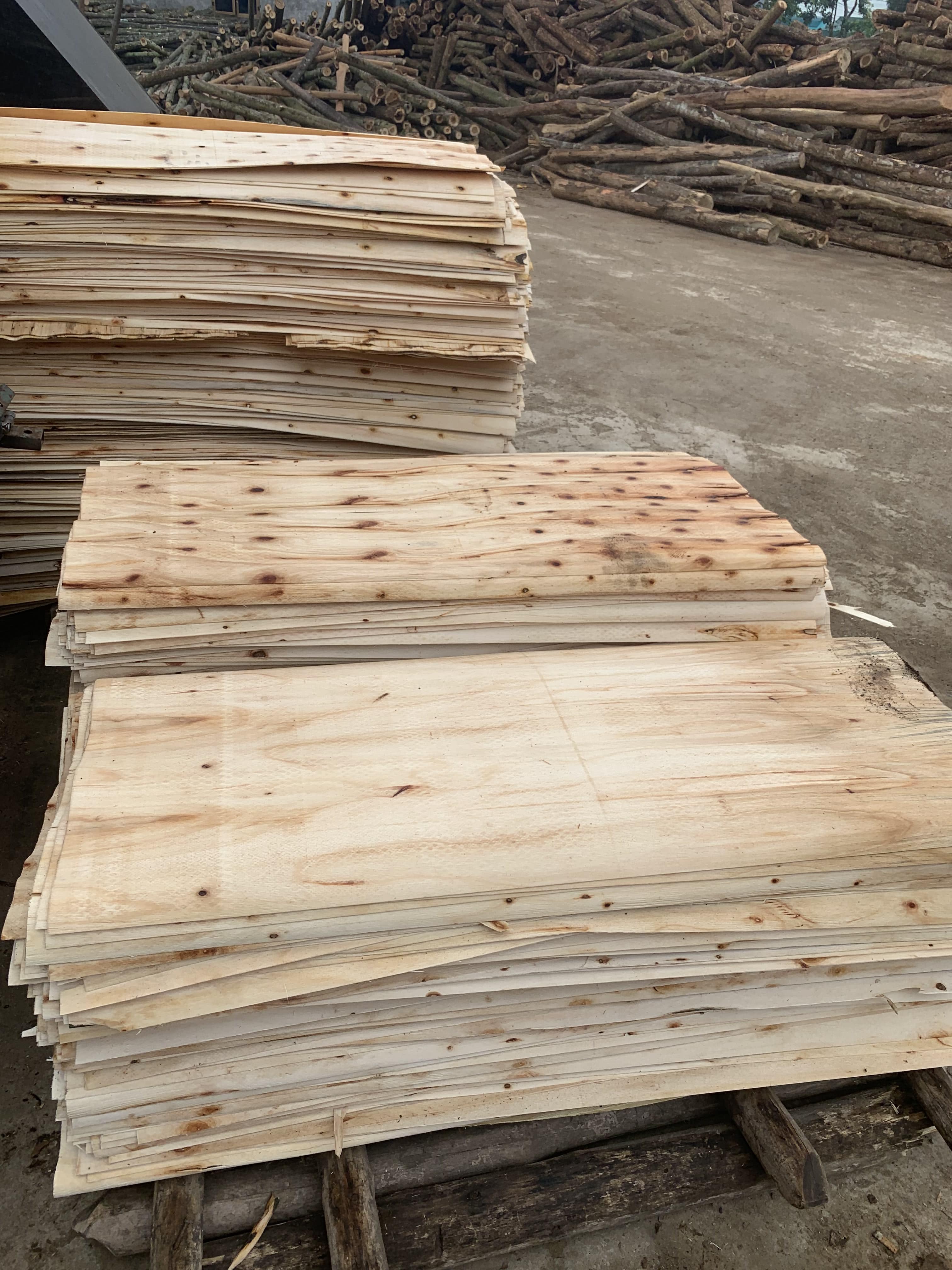
The size and quality of veneer sheets used for plywood face and core must be consistent, meeting the grading requirements according to TCVN 10316:2015. Veneer manufacturers must adhere to regulations regarding thickness variations, length, width, and criteria related to veneer defects such as live knots, dead knots, wormholes, decay, etc.
At Hachinet Takumi, veneer is classified into grades A, B, C, D, F, corresponding to increasing surface defect points. Grade A, B, C veneers are usually preferred for surface veneer layers due to fewer defects and beautiful wood grain. The remaining grades are often used for the core or surface lining layers.
After completing all the above steps, veneer sheets are packaged according to their grades. The sheets are stacked in a certain quantity and accompanied by complete information about grading, wood species, moisture content, dimensions, production date, etc. The packaging process is carried out to ensure safety and prevent damage to the veneer sheets.
If you have a need for veneer, please contact us
Email: order.takumi@hachinet.com
Tel/whatsapp: (+84) 367 622 386
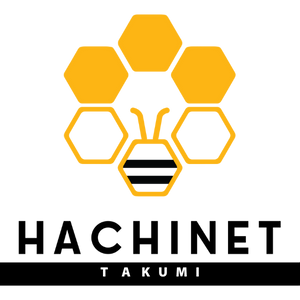